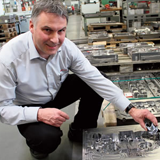
Fast, safe and lower cost - WORKNC simplifies 5-axis machining at Meissner AG
Investing in 5-axis machining
Meissner AG, one of Germany’s largest independent tool makers, has invested heavily in 5-axis machining, which has given it a significant competitive advantage, and WORKNC CAM plays a very important role by making CNC programming easy, fast and secure. Tilman Löffelholz, CEO at Meissner AG says, “14 of our 26 milling machines are capable of simultaneous 5-axis machining. This is our focus now and, in most cases, we can achieve lower costs and shorter lead times than could be achieved with 3-axis machining.”
“We have worked very successfully with some very large geometries and it is very fast. If you use WORKNC V21 with parallel processing on a powerful PC with 4 or 8 cores, the results are fantastic”
Thorsten Koch, Team Manager
Staff-owned company provides quality and service
The company has been using WORKNC since 1996 and since then it has tripled its turnover and now employs 300 people. Tilman Löffelholz says, “Because the company is majority owned by its staff all our employees are extremely motivated and pride themselves in their high skill levels. This fosters an entrepreneurial and responsible attitude which is reflected in the exemplary quality and service we offer to our customers.” Specializing in the automotive sector the company produces tooling for the casting of engine blocks and cylinder heads, blow molds for fuel tanks and tools for the production of interior trim panels.
5-axis programming made easy
According to popular opinion 5-axis CNC programming is difficult. Thorsten Koch, Team Manager, dismisses this argument. “With WORKNC, 5-axis programming is no more difficult than 3-axis programming. When we chose the software in 1996 its simple operation, high reliability and collision free toolpaths convinced us that it was the best. Over the intervening years much has changed in machining technology and WORKNC has been at the forefront of innovation.”
The company uses CATIA, Siemens NX and Pro Engineer CAD systems. Thorsten Koch says, “User friendly and simple interfaces to CAD make it easy to manipulate our models. New CAM programs are almost always 5- axis now and we use both WORKNC’s Auto 5 and its direct 5-axis strategies to produce toolpaths. Auto 5 automatically creates 5-axis toolpaths from 3-axis cutterpaths. By simply adding the details of the tool and its holder, the software produces a collision free 5-axis toolpath while considering the kinematics of the individual machine tool.”
Tooling costs cut in half
Reinhard Hackler Mechanical Production Department Manager expands on the advantages of 5-axis machining. “We have completely eliminated operations such as EDM, electrode manufacture and reclamping which has resulted in huge savings. We also achieve a better surface finish and improved accuracy through the use of shorter tools which give us improved chip removal and reduced cutter deflection. Vibration is less too, enabling us to use smaller diameter tools and finish more of the part in one operation.”
He continues, “For machining one of our sand casting molds for engine blocks, we might use 4 to 6 tools in the 5-axis finishing operations. To do the same in 3-axis would require twice as many tools. The reduced number of tools and the longer tool life we achieve through low vibration levels has cut our tooling costs in half when compared with our previous 3- axis methods.”
Check & Go
Meissner AG likes the WORKNC Check & Go functionality which simulates the toolpath after calculation but before postprocessing. The software takes into account the axis orientation for 3+2 and 5-axis machining, the machine geometry and kinematics, the tooling and the position of the part on the table, detecting and marking any potential collisions. Thorsten Koch says, “If an out of travel limit is reached, WORKNC can calculate the optimum location for the part on the table which in many cases enables us to overcome the problem and machine the part in one operation, avoiding the need to re-clamp the part.”
Simulation ensures security
The company now has 16 WORKNC licenses of which 9 are 5-axis. In addition, it has 16 WORKNC viewer licenses in the workshop next to the machines. Reinhard Hackler says, “The viewer software allows our engineers to visualize the component drawings and the toolpaths for upcoming jobs, minimizing paper and improving confidence and performance.” The engineers agree, “On the new complex milling programs we are working with, WORKNC’s simulation ensures a high level of security for the whole machining process.”
Fast speed of calculation
5-axis programs are large and the CAM system needs to create large volumes of CNC code, so speed of calculation is important. Meissner AG uses WORKNC V21 which is 64- bit and includes parallel processing and multi-threading, enabling the system to easily manipulate and manage extremely large files. Thorsten Koch says, “We have worked very successfully with some very large geometries and it is very fast. If you use WORKNC V21 with parallel processing on a powerful PC with 4 or 8 cores, the results are fantastic. It makes programming really fun.”
About the Company
Name: Meissner AG
Web: www.meissner.eu
Benefits Achieved
- Made big savings
- High level of security with simulations
- Able to work much quicker
Comments
“We have worked very successfully with some very large geometries and it is very fast. If you use WORKNC V21 with parallel processing on a powerful PC with 4 or 8 cores, the results are fantastic”
Thorsten Koch, Team Manager